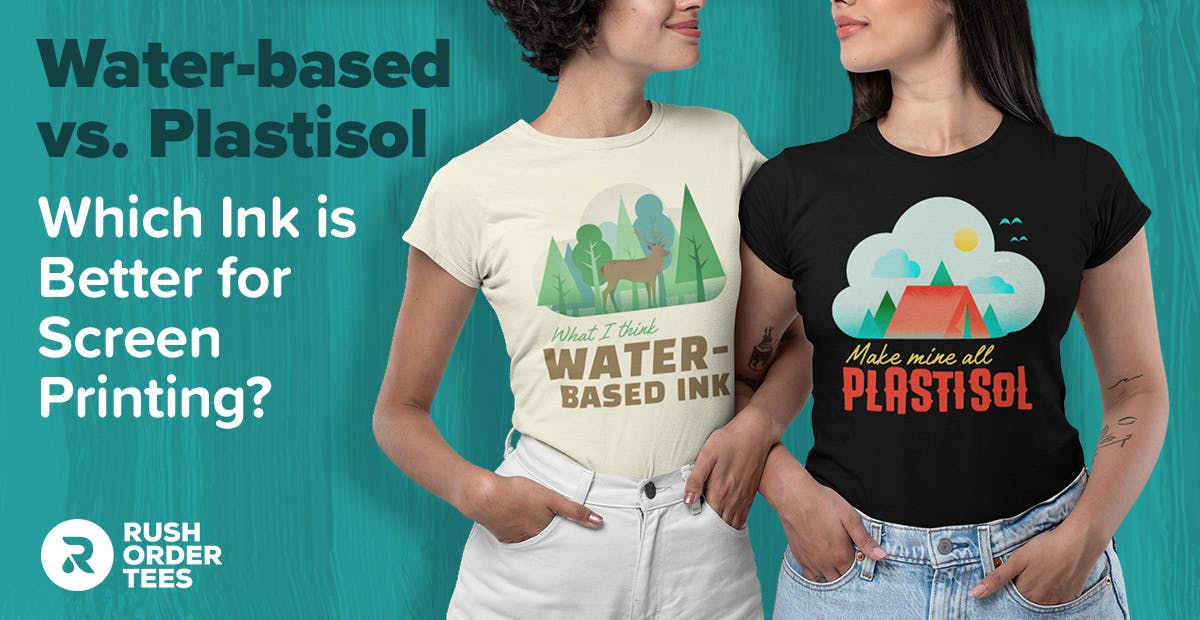
PRINT METHODS
Which Screen Printing Ink is the Best? Comparing Water-based Ink vs Plastisol

Imri Merritt
February 5, 2020
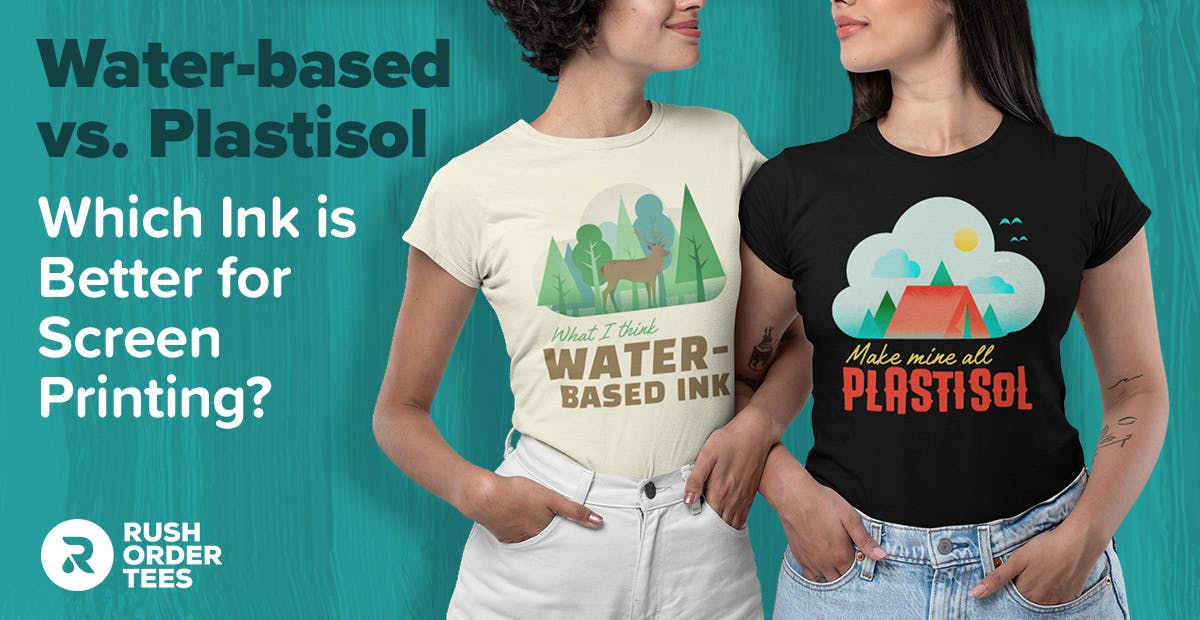
In the decorated apparel world, there are many different techniques to print custom graphics, and screen printing continues to be the fan-favorite. But there are two broad categories of inks: Plastisol and water-based. Naturally, the next question asked is: Which one is better? In this post, I’ll compare and contrast the two main types of inks to give you the answer.
Water-based vs Plastisol: Which ink is better?
Like so many things in this industry, the answer is it depends. If you have light-colored cotton shirts and you’re printing a detailed design with muted colors, water-based is the way to go. If you have dark-colored shirts and you’re printing a not-so-detailed design with bright colors, then Plastisol is your best bet. But even with such specific examples, it still depends.
Ideally, what we all want from ink is a soft and lightweight print that achieves accurate color matching along with optimal levels of vibrancy, that is breathable enough, holds the details of a design, is versatile enough to print on a variety of garments, is durable enough to stand up to years of wearing and washing, is easy to use, cost-effective, and eco-friendly.
Is there one kind of ink that can do all that? Nope. Is that too much to ask? Probably.
So the real question is not which ink is better, but rather: Which is best for which circumstance? There are many factors to consider, and for the purposes of this post, I’ve broken them down into the top eight. Keep in mind there will be different sets of considerations for different types of customers, and a different set if you’re a printer. Let’s quickly go through them.
1. Water-based ink has a softer hand (usually)
In printer speak, “hand” is essentially the way a print feels, along with its weight. The hand can be soft and light (yes please), or rough and heavy (no thanks), or somewhere in between. Water-based ink inks can produce some of the softest and lightest T-shirt prints out there, and in the best cases, there is virtually no hand– which is a good thing.
Why does water-based ink have a softer hand?
The reason is the fundamental difference between these inks. Plastisol, as you might imagine, is plastic-based. It’s made up of PVC particles or other polymers suspended in plasticizer. It’s essentially liquid plastic. And when heated to a high temperature (or cured) it becomes a solid. So a Plastisol print is a layer of solidified plastic that sits on top of the fabric.
Water-based ink, while not completely free of plastic, is mostly water-soluble and absorbs into the fabric. When this ink is cured, the water-based solvents evaporate, leaving behind only the pigmented binder compounds– less of an ink deposit than Plastisol. The hand is so soft on some water-based prints that it appears to be just dyed fabric.
The soft hand of water-based ink on darker garments is often achieved with the help of another kind of ink…
Discharge
This type of ink, often used with water-based inks, leaves nothing at all behind– in fact, it takes something away.
Discharge ink has a chemical (formaldehyde) that essentially bleaches the dye out of the garments. It’s especially useful for dark or colored garments– but can only be used effectively on 100% cotton. When you “discharge” the dye from a garment, you’re creating an (almost) white base.
Printing dark garments with Plastisol, on the other hand (or should I say heavier hand), requires a layer of white ink to create an opaque underbase to print vibrant colors. It can make for a heavier print even before layering all the colors on top. There are thinners and techniques to reduce the ink deposit, but truly soft-hand Plastisol prints are the exception, not the rule.
Bottom line: Water-based inks succeed in achieving the softer and more lightweight hand between these two inks.
But they don’t do so with flying colors.
2. Plastisol ink has better color vibrancy
Color vibrancy (brightness, saturation) is where Plastisol shines, especially on darker garments. Water-based inks can produce a vibrant print on lighter garment colors, but still not as well. When you need your colors to be rich and brilliant and pop off the print, go with Plastisol screen printing. It’s one of the reasons it remains the long-time industry standard.
The reason is similar to why it has a heavier hand: the layer of plasticized ink covering the color of the garment. Plastisol is considered a 100% solid, so every bit of it stays on the fabric when cured. This blocks the dye and creates a mostly opaque underbase to print bright, bold colors– even fluorescent colors and specialty inks such as glow-in-the-dark and puff.
Water-based ink prints on dark garments are limited in their vibrancy. Not only are the inks more transparent than Plastisol, but it’s more difficult to get bright white underbase, and using discharge will give you an off-white underbase at best, diminishing the potential for an overall vibrant print. Colors tend to appear more muted, which is usually desired.
One exception is the ever-popular vintage look, and water-based inks are a great way to get it. As long as you don’t need your colors to be vibrant, you can enjoy all the benefits of a soft-hand print. Throw in a custom distressed texture and you have the trifecta of the vintage look: muted colors, soft hand, and a worn, aged look to the print.
3. Plastisol ink has better color accuracy
For the same reasons that colors are more vibrant with Plastisol inks, color matching can be achieved down to a specific Pantone shade. When your print colors need to be exact (let’s say for the purpose of branding consistency) Plastisol is the way to go. No matter the shirt color or the type of fabric, if you need the color to be bright red 185 C, that’s what you get.
With water-based inks, results may vary. Improvements have been made over the years, but not enough to beat Plastisol. The difference in vibrancy alone can account for a color being a few shades off. And that’s before you factor in other things like color shifts due to dye migration, curing, press conditions, if Mercury is in retrograde, and everything else.
4. Both inks are extremely durable
This one could be argued from both sides, so I’m calling it a tie. There are many factors that contribute to a print’s durability. Because of the way water-based inks are absorbed into the fabric, the print should hypothetically last as long as the garment does. And because Plastisol is permanently bonded to the surface, it should also last as long as your T-shirt does.
That being said, if a print is not cured properly, no matter what type of ink used, it will affect the durability. Other factors such as the quality of the ink and the type of fabric also play a role. The biggest factor by far is the treatment and care of the garment itself– if you wash with hot water, heavy detergent and bleach every week, neither print will hold up well over time.
5. Water-based ink has better breathability
Breathability, although it sounds like it has to do with airflow, is more about the ability of moisture to move through the fabric. And because water-based inks absorb deeper into the fabric, many of the openings between the fibers are left open. This gives water-based prints more breathability than a Plastisol print– which tends to plug up those tiny gaps.
Thick layers of Plastisol making a large, solid print is sometimes jokingly referred to as a “sweat patch”. Since none of the solution evaporates during curing and the plastic compounds bond to each other, it can create an impenetrable plastic surface that doesn’t let moisture or air through it. Hence the sweat patch. Here’s a short test demonstrating breathability.
6. Plastisol ink has greater versatility
By versatility, I mean the flexibility to be used on different fabric types, with various types of inks and additives, and under different press conditions. If this sounds like an important factor, it is– especially for printers. And it’s one of the main reasons why Plastisol has remained the industry standard for decades, even as digital DTG printing is nipping at its heels.
You can print Plastisol on just about anything. (That doesn’t mean you should, but you can.)
Water-based inks, not so much. They are best suited for 100% cotton textiles. With blended fabrics, you start running into some difficulties because the synthetic parts of the fabric don’t absorb the ink the way cotton does. And if you’re printing water-based inks on straight polyester, you’re gonna have a bad time. It gets real tricky real fast.
Bottom line: Your garment options are going to be limited if you want a high-quality water-based screen print.
7. Water-based ink is more eco-friendy (slightly)
Lately, there is a big push towards “eco-friendly” production methods, led by the Consumer Product Safety Information Act (CPSIA), along with some major brands, in an effort to reduce the use of PVC and move away entirely from phthalates (an even more toxic polymer). Because of this, major players in the industry are marketing water-based inks as a solution.
How much better for the environment are water-based inks?
The answer (as usual) is it depends. Each ink has a different environmental footprint, and there are trade-offs with water-based ink that negate some of the positive attributes being touted by ink manufacturers. And some of the claims being made, especially pro-waterbased and anti-Plastisol are questionable at best.
This might be a good time to point out that water-based inks also contain plastic, in the form of acrylics and other binders.
And while water-based inks are PVC-free, they rely on solvents that evaporate, leaving the pigmented binder compounds on the garments. The primary solvent is water, but they often contain co-solvents such as formaldehyde and alcohol. These co-solvents can be harmful and put printers at risk unless they are properly protected from the evaporative fumes.
Also, water-based inks generally require more energy for print shops to use. Driving out moisture in the curing process can take much longer than Plastisol. And they generally have a lower yield than Plastisol– and therefore more waste, which often (and mistakenly) gets poured down the drain. But Plastisol waste, once cured, can be disposed of like regular plastic.
This is not to say that dried ink ending up in a landfill is fine, but to emphasize that water-based waste is not much better.
What’s bad about PVC?
Polyvinyl chloride, commonly known as PVC, and even more commonly known as vinyl, seems to have gotten a bad rap over the years. Of course, there are some obvious issues with it, as there are for any mass-produced chemical product. But from what I can tell, many of the charges against it are overblown and have been debunked.
“PVC is extremely low maintenance, easily recyclable, and it doesn’t off-gas or leach harmful chemicals if it comes in contact with water. In addition, the PVC manufacturing process does not require a great deal of energy and the PVC itself is lightweight, which dramatically cuts down the carbon footprint of producing and shipping PVC products.”
PVC continues to be one of the most useful and ubiquitous plastic products in the world, across a variety of industries. Nevertheless, the push is on to replace this compound in inks, as there are alternatives showing some promise. But until those alternatives can match the versatility, consistency, and reliability of Plastisol, it’s not happening anytime soon.
Bottom line: how “green” a print shop is has much more to do with how it’s managed than which kinds of ink it uses.
8. Plastisol ink has a lower cost (usually)
Soft-hand prints are all the rage these days, so water-based ink is enjoying a resurgence for that reason alone. What people may not realize is that comes at a higher price. Many printers even price it as a premium or specialty ink. There are a multitude of difficulties with it (see below) resulting in additional costs that will often be passed along to you.
That being said, shops that specialize in water-based printing are able to reduce these costs. On top of that, there’s a lot of competition out there so prices will vary from printer to printer. Here at RushOrderTees, we like to keep our prices competitive.
PRO TIP: Plastisol ink is easier to use and has a higher yield
As a customer trying to order T-shirts for your flying trapeze team, these will not be a factor for you. If you’re a printer, they are. Plastisol stays stable for the most part and therefore keeps its workability. It’s also fairly straightforward as far as getting a job done. For most jobs, you can go right out of the bucket, to the screen, to the shirt, to the dryer, to the box.
Water-based inks are generally harder to work with. They have high viscosity and many things that can go wrong.
For those reasons alone, lots of print shops don’t even bother with water-based printing. There are different complications and formulas for different types of garments, so as a printer, you need to know what you’re doing. To avoid problems you have to use things like low-cure additives, dye blockers, and “high-solid” acrylic inks. Plus it starts drying out. (No pressure!)
RushOrderTees recommends: Plastisol
My overall verdict between these two inks is that Plastisol comes out on top. It’s versatile enough to print on any garment with full-color vibrancy and accuracy. It can achieve photo-realistic simulated process prints and supports a wide variety of specialty/special effects inks. It’s affordable, long-lasting, and can be printed without leaving a heavy hand.
Check out the infographic below for a summary of this post. When you’re ready to create your own design and order some custom printing, start right here and get an instant quote today.

Imri Merritt
About the Author
A graduate of the Multimedia program at the University of the Arts in Philadelphia, Imri Merritt is an industry veteran with over 20 years of graphic design and color separations experience in the screen printing industry.